Habor´s R&D facilities are located in their headquarter in Taichung. Every model is tested in modern test chambers until 100% functional capability and performance can be guaranteed.
Habor continuously strives for developing cutting-edge technologies in order to reduce the energy consumption of their cooling units. This reflects for example in the introduction of sensor-controlled fans and in the usage of the latest refrigerants to minimize the compressor capacity. Vertically assembled fans further reduce the loss of coolant.
The loss of efficiency caused by cooling adds up to 30% of the power consumption of the machine tool. Therefore, savings regarding the cooler model size are essential. The customized adaptation of cooling units already pays off at a volume of 10 coolers per year. The optimal layout of customer-specific coolers will be detected by load tests in the environment test chamber. Customization of the electronic control is possible as well.
Habor´s developments:
PID V Series: high-precision PID control can regulate the coolant temperature with a precision of +/-0,1 K
DC inverter cooler: enables additional savings in power consumption
Environment test chamber
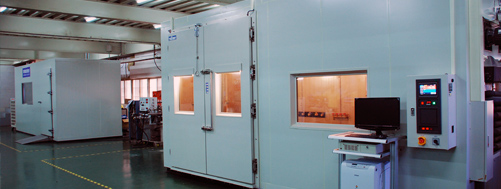
To ensure that their products meet the requirements of customers in every region of the world, every cooler model performs tests in an environment test chamber with adjustable ambient temperature and humidity.
Electronic test devices
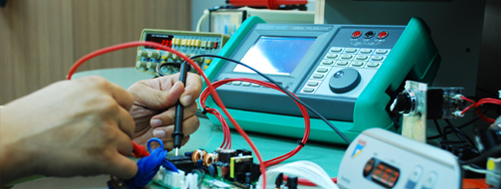
Habor uses modern electronic test devices to ensure that their products fulfil the demanding industry requirements regarding precision and reliability.
Professional R&D team
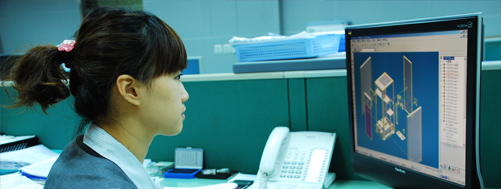
Habor´s professional R&D team provides integrated and application-specific cooling solutions to its customers, for example regarding temperature control, tank volume and coolant flow rate.